Lightweight design and Design for manufacturing usually don’t go hand in hand and there is considerable truth to that statement. And increasingly every industry out there is on a search to increase the efficiencies and one of the ways to do it is by decreasing the weight. Newton’s second law can tell you why that is so. Acceleration is inversely proportional to the mass. The implication is that it requires considerably more energy to accelerate a heavier object than a lighter one. And this has been known for centuries. What is new is the newer design optimization techniques which can help you reduce those excess mass and companies are also trying to differentiate their product in the market with their pursuit of higher efficiencies. The pursuit of lightweight is extremely rewarding, especially in the modern world. We are on our way to electrifying our vehicles, we are thinking about hyper loops and more efficient air travel. And above all, we are increasingly environmentally conscious. Lightweight design helps us in all of that. Electric vehicles, extremely ranging sensitive to weight, rewards the pursuit of less weight. The advantages of less weight Aerospace industry are even more obvious because there are millions of dollars per year worth of fuel savings directly associated with it. The bottom line is “Pursuit of lesser weight” is worth it. But the argument is whether lightweight design should be prioritized over design for manufacturing. We don’t think one has to be prioritized over the other and design for manufacturing is important too. DFM is no slouch. If not paid due attention, DFM can potentially blow the costs through the roof. The other reason to give importance to DFM is that you cannot scale up the manufacturing that efficiently if the parts are no designed concerning DFM rules. Agreed, Lightweight design and Design for manufacturing are two disparate design foci. But they are not necessarily contradictory. Up to a certain extent, Lightweight design can be done without compromising on Design for manufacturing. The first step to weight reduction should not be focused on the parts themselves; as a matter of fact, it should be considered the last. The first phase of weight reduction is what we can call “System-level weight reduction”.
Systems-level weight reduction
This should perhaps be the first step in going towards lesser weight as this is the easiest way to reduce weight from a manufacturing standpoint – and great from the design point too. It is just a way of saying “reducing weight from a holistic perspective”. Common ways of doing this include re-arrangement of the parts in a system to reduce the structure weight, clubbing two or more parts into one, and trying to go monolithic. A small thumb rule to reduce the weight of a system is to reduce the number of fasteners and by the extension number of parts. This is easily the most efficient way to reduce weight.
Material level weight reduction
The second step in weight reduction is to do a proper material selection. This doesn’t mean going for the most exotic metals and composites available and it is not feasible too. But prudent material selection can save us a lot of weight. For example, let’s talk about Aluminium and Steel. Just because Aluminium is about three times less dense than steel, it does not mean replacing Steel with aluminium makes the part three times lighter. Steel is almost three times stronger than Aluminium and so strong to weight to ratio is almost the same. But it also doesn’t mean steel and aluminium are replaceable.
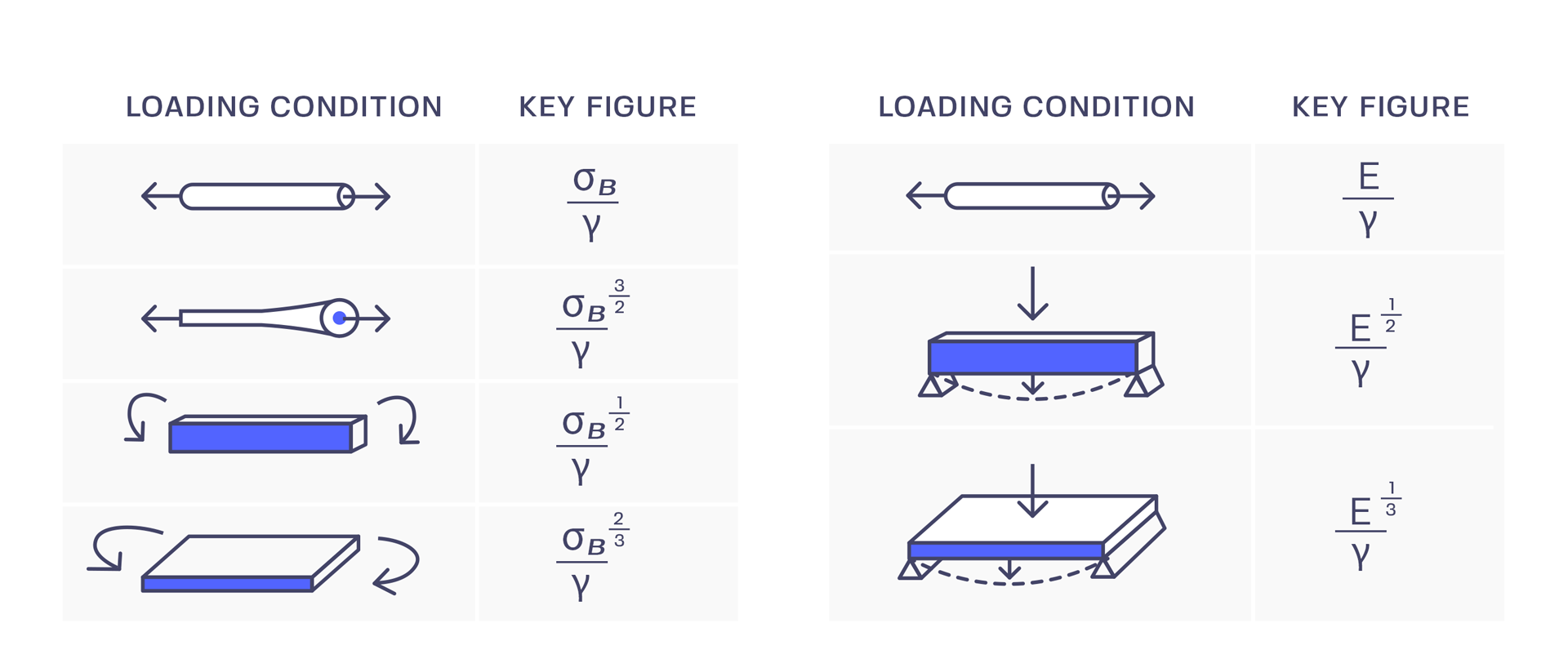
The thing here is Steel is much stronger than Aluminium in tension because of its high higher tensile strength relative (Young’s modulus) to weight. And in Shear, Aluminium is relatively stronger than steel concerning weight. So, for a part of a structure that is exposed to high tensile loads, using steel instead of Aluminum reduces the weight by 3%. Similarly, using Aluminium instead of Steel in a pure bending condition reduces the weight by 40%. Similar weight reduction percentages can be calculated for different load conditions. This is because of the changes in material property requirement for a given load condition that is expressed here as key figures for certain load conditions. This is not just limited to Steel and Aluminium. This can be done for composites, exotic metals, and plastics too. It's all about the relative strengths in tension and shear. What I am trying to imply here is that going for the most exotic materials won’t probably reduce weight as much as you might think but it is a sure-fire thing that it will skyrocket the costs. But wise material selection can help you save more weight than you can when doing weight reduction compromising on DFM.
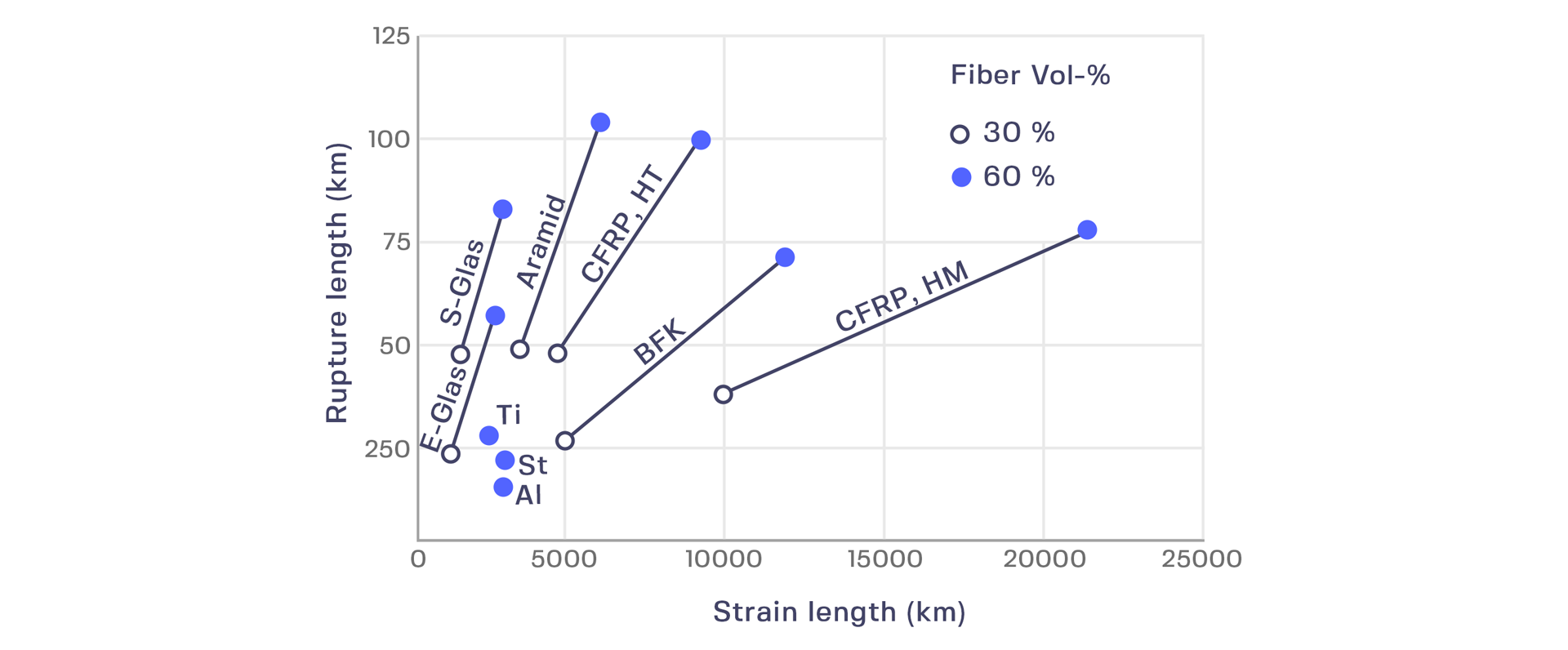
Part level of weight reduction
This is where you might come upon compromising on DFM. But that is not necessarily always the case. Up to a certain extent, you can do this without impeding DFM. The problem with this type of weight reduction is the percent of weight one can reduce from a system. I agree, that in the end, it all adds up to give us better numbers, but still, the cost benefit ratio for this kind of weight reduction is kind of low. But still, we are in a world that is continuously searching for performance and efficiency. So, we must pursue this path too and there are a few thumb rules one can follow to do this well. Basic tenet of this method is to exploit the full load carrying capacity of the material.
Increase the second moment of inertia where the stresses are higher
To explain it a little bit deeper, add material where you have the most stresses in a way that increases the second moment of inertia and remove where you don’t have a lot of stresses. This simple statement possibly embodies what it means to reduce weight from a structure. Increasing the moment of inertia without increasing weight is the best way for this. For a cantilever structure, it means it adding material near its fixed support and removing material near the ends. And the material must be added in the same axis as the acting load thereby increasing the moment of inertia.
Design the structures for tension
Most metals perform incredibly better in tension than in any other load condition. It all has to do with stability. In tension, it creates a stable elongating deformation which is linear with load, whereas with bending of compression (Buckling), it creates an unstable bending deformation that is non-linear with the load. That’s why it is incredibly efficient to design with tension. Look at the most efficient structures like suspension bridges, spoke wheels, even actuating cables, they work on tension.
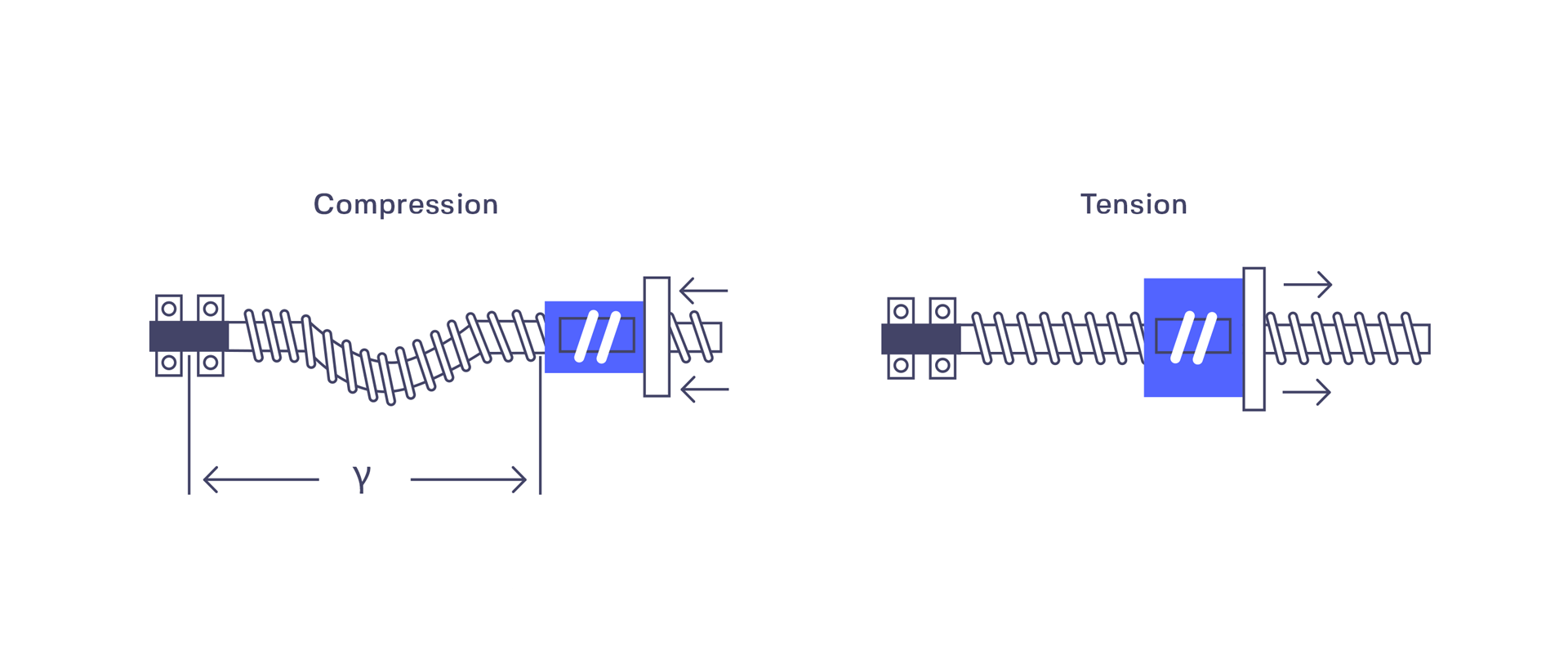
Design “perfect” structures – Not redundant, not deficient
This statement is not just true for trusses; it can be applied to all other structures too. A deficient structure can make the system unstable forcing you to add more material to it and a redundant structure is too stable and you cannot remove enough material from it. A perfect structure is just ideal for the most optimized weight for the given load condition.
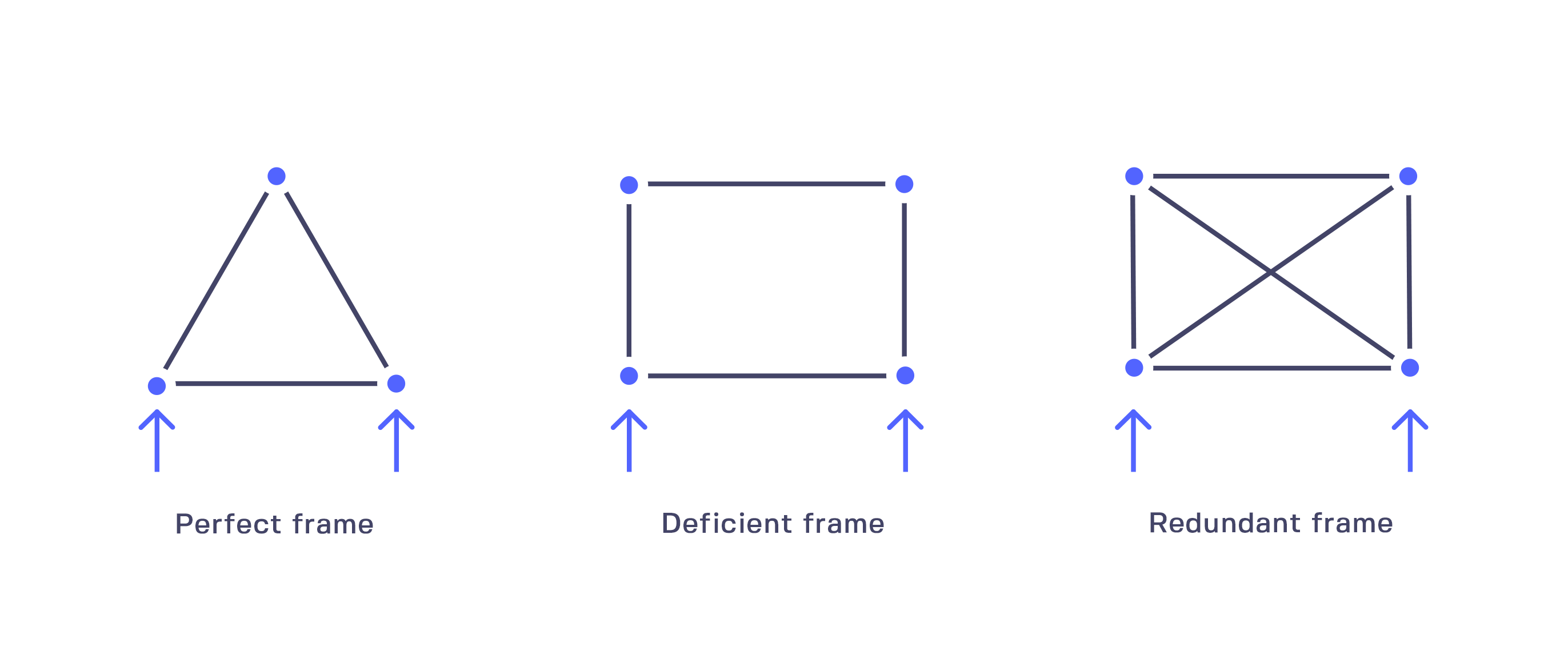
Despite going through all this, you might still need to reduce more weight. That’s when you can impede DFM for better performance. And with the fields of Generative design and Topology optimization developing fast, we might be able to design the most efficient structures which might be manufactured by the additive manufacturing process. But till that can be done for scale, we have to give due importance to DFM while designing lightweight structures.