Most metals and their alloys always try to revert to their natural form by oxidation or sulfation, and we call the process corrosion. Corrosion erodes the structural, mechanical, and aesthetic properties rendering them useless and it causes billions of dollars of damage every year. And it is for increasing the corrosion resistance, we are doing post-processing processes like anodizing, electroplating, chem coating, and powder coating on our parts. In addition to increasing the corrosion resistance, these processes also make the finished parts look better, aesthetically.
But one has there are several post-processing process options at his/her disposal, and they could potentially cause some confusion. Choosing the right process for the application is very crucial for the performance of the part in the long term. In this article, we want to clarify the application of each post-processing process and help you chose the best process for your application.
At Custiv, we have several post-processing options available. The most common ones are
- Anodization
- Powder coating
- Passivation
- Electro-plating
- Electro-polishing
- Chem-coating
Anodization - Type 2
Anodizing is the process used to increase the thickness of the natural oxide layer on the metal surface. It increases the corrosion resistance of the material. Type 2 Anodizing process involves dipping the Aluminium part into sulphuric acid and creating a thin oxide layer on top of and into the Aluminium surface. This creates a corrosion-resistant and hard surface. It also gives a lustrous appearance to the part. This type of anodization can also be coloured with virtually any colour.

Anodization type 2 coat is very thin (1 – 25 micron) but still they provide really good enough corrosion resistance. The anodized surface is also an electric insulator, making them ideal for many electric applications. This coating is good enough for most common aluminium applications, including household items, decorative parts, electronic gadgets, etc.
When to use Anodization type 2?
When you need fairly good corrosion resistance for Aluminium parts, Anodization type 2 is best for your part. Anodization can also be made for a few other materials, but the process is best for Aluminium and its alloys. It can also be coloured and the surface appearance will also be good, so it can be used for decorative parts.
Anodization Type 3
Anodization type 3 – also called Hard coat – is much similar to type 2 anodization in as both use sulphuric acid and both create a natural oxide layer, but type 3 anodization creates a much thicker coat. Anodization type 3 forms a layer of over 25 microns on the metal surface – half of the thickness forms over the base metal surface, the other half of the thickness is formed over the base metal surface. Because of this thickness, this process can only produce dark grey-coloured parts and they are extremely hard and abrasion-resistant.
When to use Anodization type 3?
This thicker anodizing process is most appropriate for Aluminium parts. The outer anodized surface will be very hard and abrasion-resistant, so can be utilized for industrial parts that demand those extreme properties. This process produces a dark grey coloured layer on the part and this anodized surface cannot be dyed with any colour other than black. So, it is predominantly used aesthetics is highly prioritized.
Powder coating
Powder coating is a process of electrostatically coating a dry powder-based paint and then curing with heat or UV light. It can be used to coat a variety of materials including metals, composites, even certain plastics. It creates a hard durable coat over the material surface, making the base material impervious to environmental damage, thereby reducing corrosion. It comes in virtually all colours and it creates a more uniform coat than most painting processes.
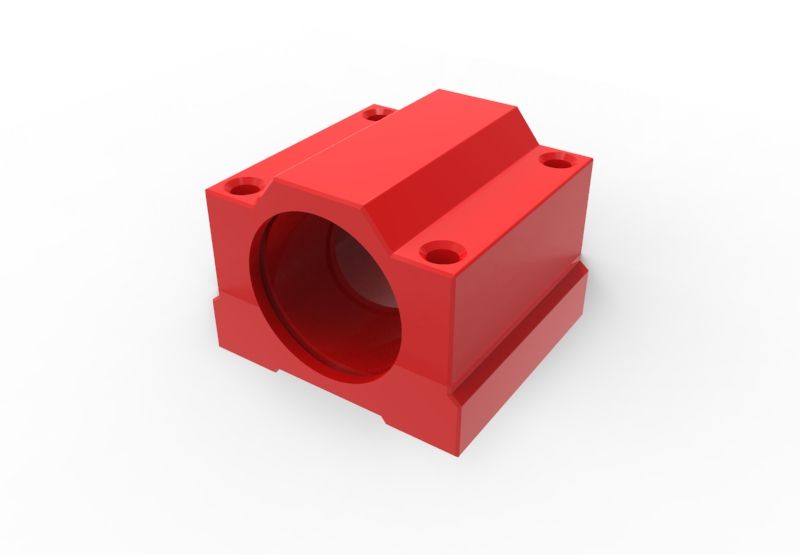
When to use powder coating?
Powder coating is more of an aesthetic improving process than a functional one. Despite that, it still offers a certain degree of corrosion resistance, as the coat can keep the elements at bay. In addition to that, powder coating can also be done on a wide variety of metals. So, powder coating can be used for used in a wide variety of applications where the aesthetic is of higher importance.
Passivation
Passivation is a process of chemically creating a thin oxide layer on the metal surface, making the metal passive to corrosive chemical reactions, hence the name. Unlike anodization or Electroplating, Passivation is a chemical process. Prior to passivation, the material’s surface must be cleaned off any foreign entities for a good passivation process. Then the part is placed in an acidic passivation bath for a certain time. This process does not give any colour to the part.
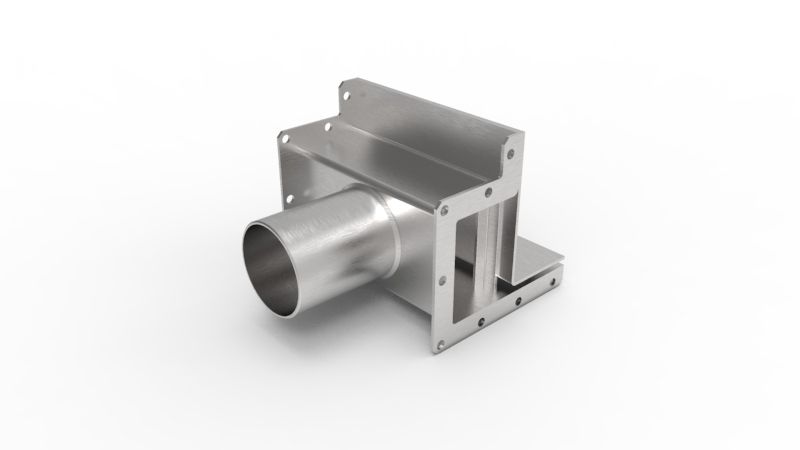
When to use passivation?
Passivation is a process that is commonly done for stainless steel parts. It can be done for a few other materials, but it is most effective for stainless steel. The passivation process also does not alter the appearance of the part very much. So, more often than not, if it is a stainless-steel part, passivate it.
Electroplating
Electroplating is the process of coating a different metal over the base material. The part to be coated is placed as the cathode and the electrode as the anode. During electrolysis the anode material deposits uniformly on the cathode. It is mainly done for increasing the corrosion resistance and augmenting the appearance of the part.
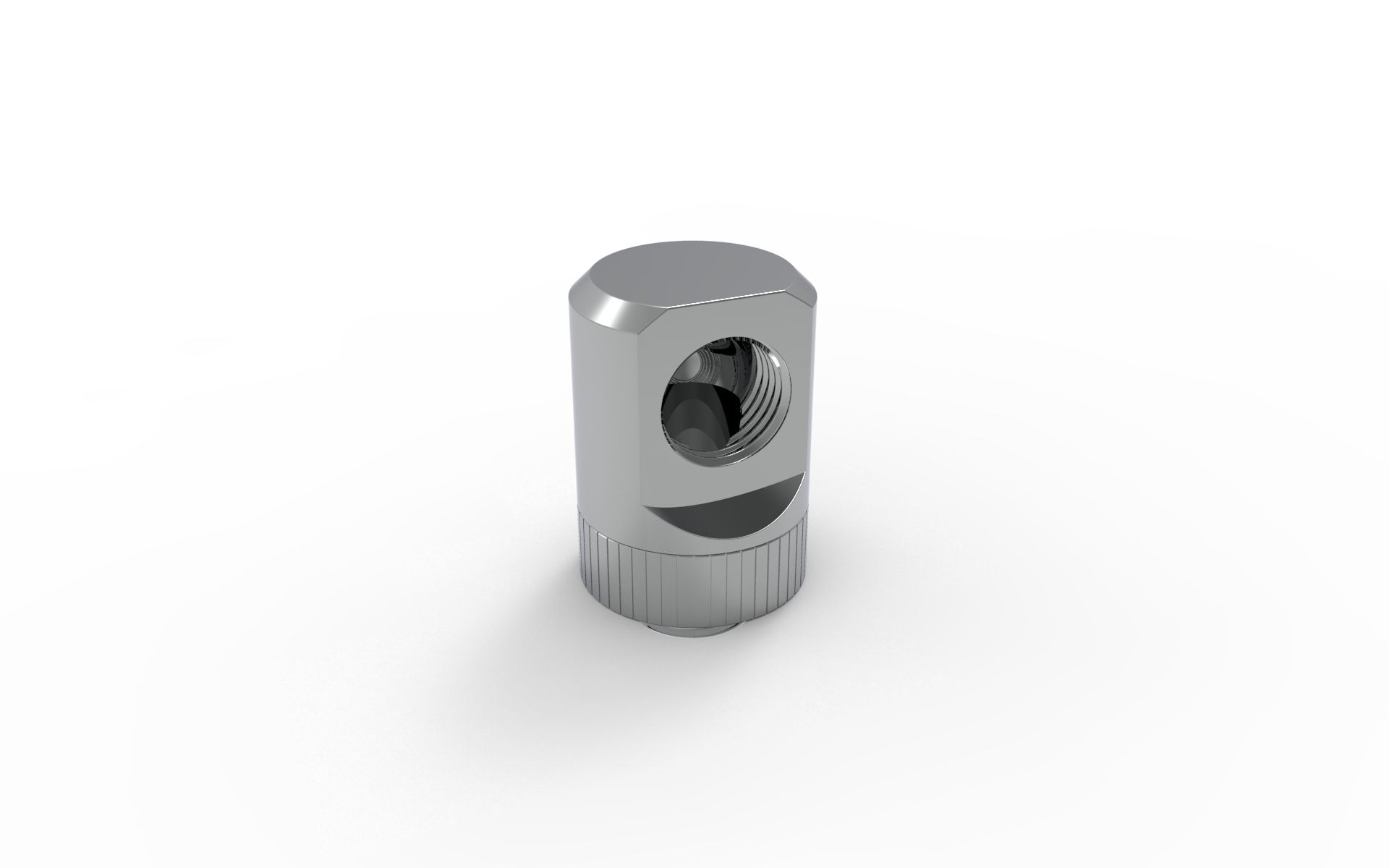
When to use Electro-plating?
As you are practically coating one metal over another different base material, it comes with a wide array of advantages. For one, electroplating can be used for both aesthetic and functional purposes. If the required material is expensive and difficult to acquire, you can do the next best thing by plating the material on a more common base material. For example, gold and silver plating is predominantly used in jewellery for its aesthetics, whereas certain applications require platinum and palladium plating for their catalytic properties. Zinc is also coated (galvanization) to increase corrosion resistance. Chrome plating is another common electroplating process that is done for its mirror-like finish aesthetic.
Electropolishing
Electropolishing is the process of electrochemically removing a thin outer layer from the base material to give the part a more lustrous aesthetic. It is practically reverse electroplating. That is, our part is made the anode and different material is made the cathode. So that the material of our part gets coated on a random cathode, removing a thin upper layer. It can be controlled to very small thicknesses (20 to 40 micron) and the biggest benefit that this process offers is that it can remove the material uniformly over the entire surface area of the part.
When to use electro-polishing?
It does not improve the corrosion resistance of the part; in fact, it reduces it. This process can be done for most materials, but they should be only considered when the part requires a smooth and lustrous finish.
Chem-coating
Chem-coating also called chromate conversion coating or Alodine coating is a chemical coating used to improve the corrosion resistance of the part. This coating gives a distinctive greenish-yellow colour to the part and this process is commonly used to coat everyday parts like screws, bolts, tools, etc.
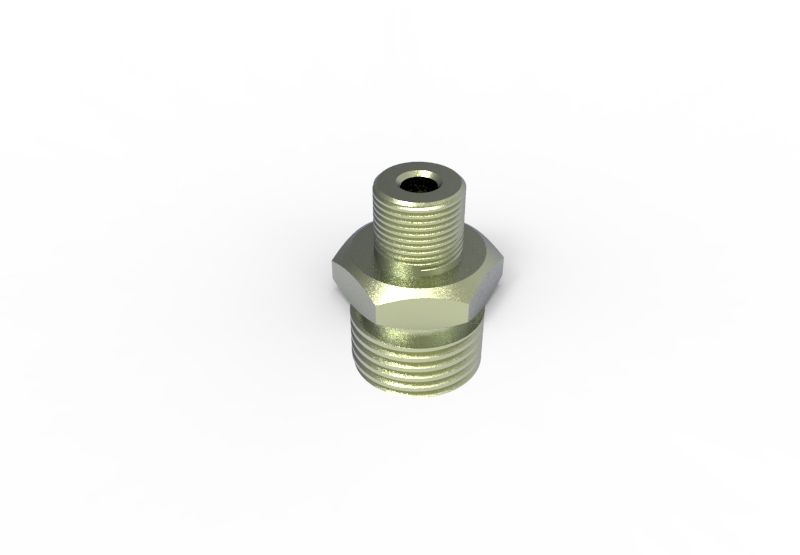
When to use Chem-coating?
Chrome conversion coating/Chem coating is an extremely important process that must be done for parts that are exposed to harsh corrosive environments like boilers, industrial equipment, tanks, etc. It is also done for parts that must be durable like tools, screws, bolts, nuts, switches, hardware, etc, to increase their lifecycle. Chem coating can also be done on several materials that include, steel, aluminium, magnesium, zinc, titanium, and copper.
Anodization type 2
- For Aluminium
- Moderate corrosion resistance
- Multiple colour options
Anodization type 3
- For Aluminium
- Creates a hard black coat
- High corrosion and abrasion resistance
Powder coating
- For a wide variety of materials
- Virtually any colour
- Mediocre corrosion resistance
Passivation
- Can be done for many materials, but most suitable for Stainless steel
- Increases the corrosion resistance
- No change in appearance
Electroplating
- Chosen based on the functional and aesthetic requirement
- Most conductive metals can be electroplated
Electropolishing
- Uniformly removes a thin layer of material on the surface
- Mostly for aesthetics or for surface finish
Chem coating
- A wide variety of materials can be chem coated
- Gives a greenish-yellow coat
- Very good corrosion resistance
- Can be performed on a wide variety of materials