Electric Vehicle Industry Growth
The millennial woes faced by the automotive sector shall receive global headwinds in the years to come. The concept of traditional toolboxes has failed drastically over years causing serious concern to the industry in capturing the future markets and meeting its standards worldwide. Start-ups have evolved to their threefold size over the years out of which North America and Europe currently hold 80% of its major activities in electric vehicles.
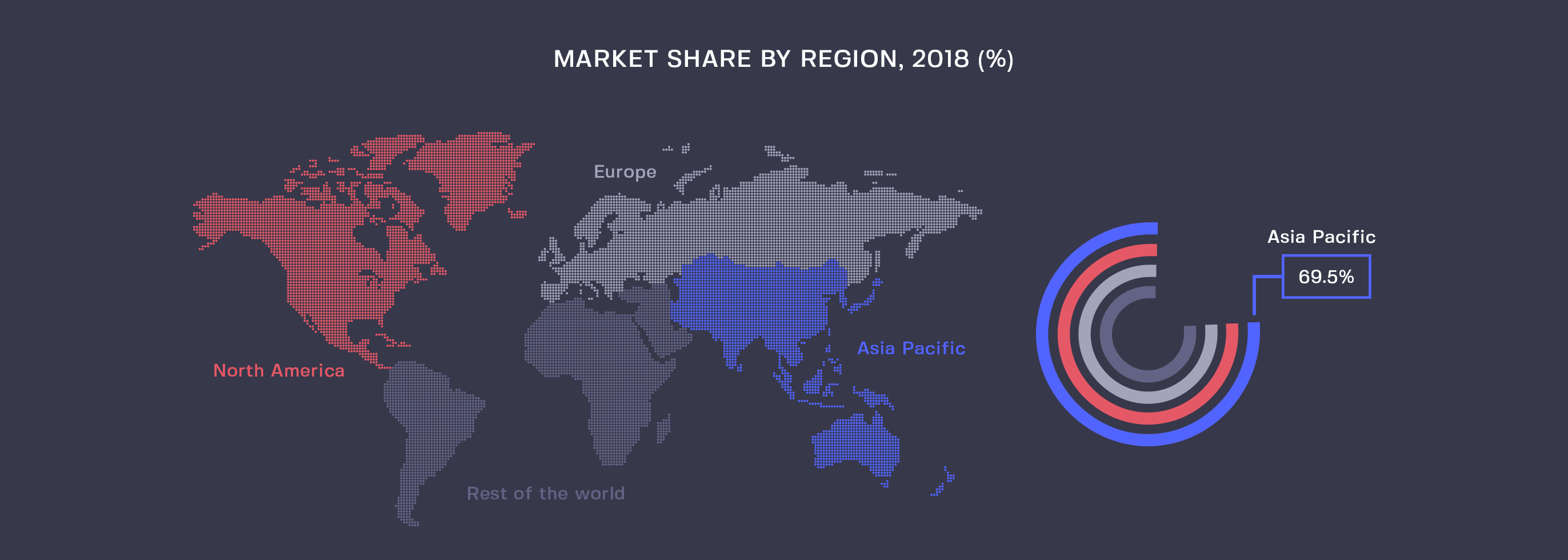
Asia shall soon offer the highest electric vehicle sales contributing to its path towards sustainability. The principal driving force in choosing the best for the environment has led to a greater number of electric vehicle start-ups. Likewise, the dream future of the automobile is said to be the Electric run vehicles but its electrifying path to bring them, in reality, is solely through its engineered properties.
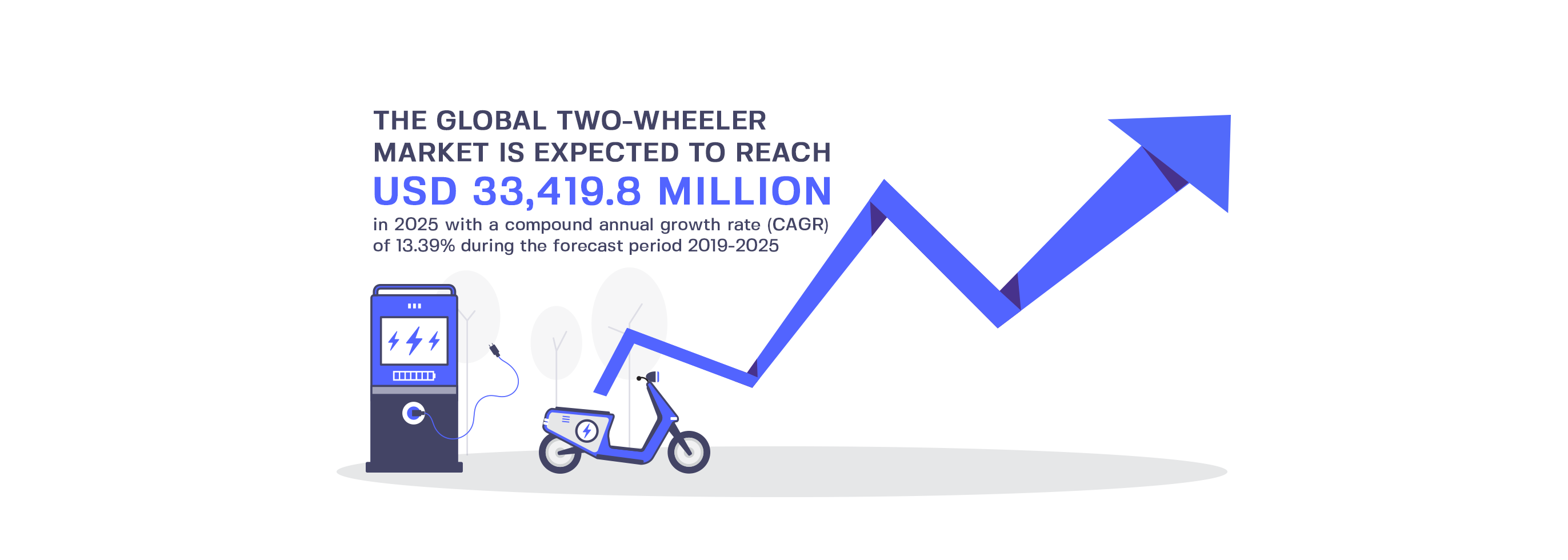
The automobile anatomy gives us a clear understanding of how polymers have slowly aced their demand in markets covering the major manufacturing essentials. They are reliable over multiple other conventional materials due to their remarkable properties offered in terms of their weight, functionality, look and feel, fuel economy, and overall efficiency. Hence to ensure the performance of the EV’s, manufacturers need to carefully select the polymers on basis of its multifunctionality traits provided.
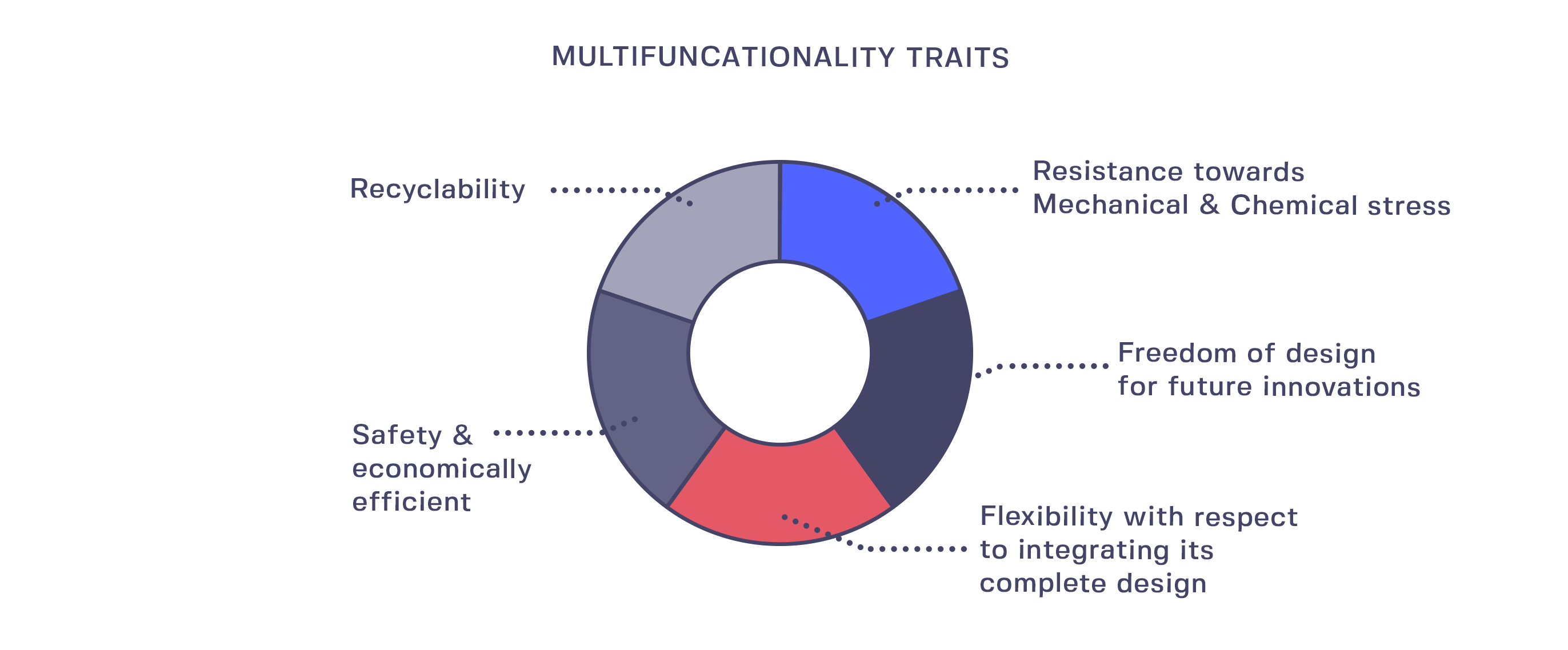
Thermoplastic polymers – King of Set and Reset actions
Thermoplastic polymers have enormous properties that can be merged with other polymers forming a polymer matrix composite. It complements one another to offer a better set of features such as wear and corrosion resistance, impact resistance, thermal resistance, stiffness, lightweight, low moisture absorption, ease of fabrication, flexibility in its design, and high resistance to chemicals and solvents. Thermoplastics are the fastest ever promising material that offers exceptional properties in automotive. They can be melt-processed, reheated, and reformed which makes handling, storage, and maintenance much easier. Owing to its applications, thermoplastics shall have a huge appeal in Electric Vehicle automotive. Polymeric composites are constantly evolving in the design of the body components. The selection of polymers in an automotive must offer a barrier to vehicle intrusion, obstruct roof crash, and enhance fuel efficiency by creating aerodynamic lightweight parts. Customers get highly influenced by looking at the aesthetics and ergonomic environment provided by the choice of polymers. With high flame retardancy, even weight distribution, and choice of variants are important to select materials that create a remarkable feel at one shot.
Listed below the polymers offering world-class properties for manufacturing Electric vehicle parts.
- Polycarbonates - Headlight, Left & Right signals lights, Meters, License plate lights, Reflectors and Rear lights.
- Polypropylene - Front panels, Pedals, Toolbox doors, Bottom covers, Handle, Rear fender, VIN plates, Hooks, break lines & reflectors.
- Acrylonitrile Butadiene Styrene - Meter covers, Mud guards & rear connections.
- Polyurethane - Seat covers, seat bucket, rear shock, cushion & Body covers.
Polycarbonates
Right from sky-high Astronauts to road ruling Drivers, Polycarbonates has been their choice of material for manufacturing vehicles exteriors offering high impact resistance, increased mechanical and electrical insulation properties, durable, high dimensional stability, and superior shatter-resistant properties that are nearly even unbreakable. Its higher resistance to creep can protect the exterior components from any rupture caused or stress applied. Its lighter weight helps improve fuel economy that can stretch even a gallon of gas. Its transparency and heat shock resistant features are utilized for headlights and shields in vehicles. Its thermal insulation properties ensure effective thermal management, especially in Electric Vehicles. Owing to its benefits, Polycarbonates have emerged from their niche role and leaving their mark in the automotive industry. Polycarbonates injection moulding processes employ rapid heating and cooling producing parts with much realistic, effective, complex geometries and part to part repeatability at the user end. The benefits offered by injection moulding over others is its excellent toughness retention at high temperatures and translucent properties. It's usually operated at a temperature range of 270° F at 264 psi.
Polypropylene
As the name suggests, Polypropylene is a pro in providing only the best set of properties that is adapted for all kinds of applications. It shall become a backbone to EV’s due to its poor conduction of electricity and be suitable for making capacitors and audio equipment. They possess high melting points and are resistant to chemical solvents, acids, and bases. They are highly resilient and act as a binder to natural composites. Its rugged and slippery surfaces mainly find their usage in bumpers, gears, panels, etc. Essential parts in EV’s such as brakes get to corrode eventually but Polypropylene’s high levels of corrosion resistance are unaffected by most organic solvents and gases such as Co2. The recyclable polymer can be easily recycled creating a lesser environmental impact. Its economic feasibility, lightweight, and versatility have always kept this material on top and preferred widely. Polypropylene is easily processed by injection moulding despite its semi crystalline nature. The processing temperature is usually between 200 to 250 degrees owing to its high melting point. Its MFI (melt flow index) values depict its ease of flow properties. Its pseudoplastic nature is appreciable for its high shear rates. Its shrinkage values are also much lesser making it suitable for most of its applications.
Acrylonitrile Butadiene Styrene
Acrylonitrile Butadiene Styrene, (ABS) is the ABC of the polymer family offering significant properties such as high impact resistance, rigidity, heat and chemical resistance, abrasion and stain resistance, high dimensional stability, weldability, and offering good surface brightness. The shiny sleek surface offered by this polymer is much suitable for designing each part. Its increased electrical insulation and heavy-duty applications help the body absorb and redistribute energy during an impact faced. Its structural strength and stiffness feature are offered due to the chemical chains that attract each other and bind together making it stronger.
Its lower melting point makes it easier for the injection moulding process. Its fluidity property after heating influences the moulding temperature and pressure, thus improving the overall performance of the moulds. It is very important to maintain the overall temperature of the slots constant as butadiene tends to become sticky with its increasing temperature. As viscosity is very high for ABS, even moderate injection speed yields a good finish. The moulding is operated at a temperature between 180-240 degrees C.
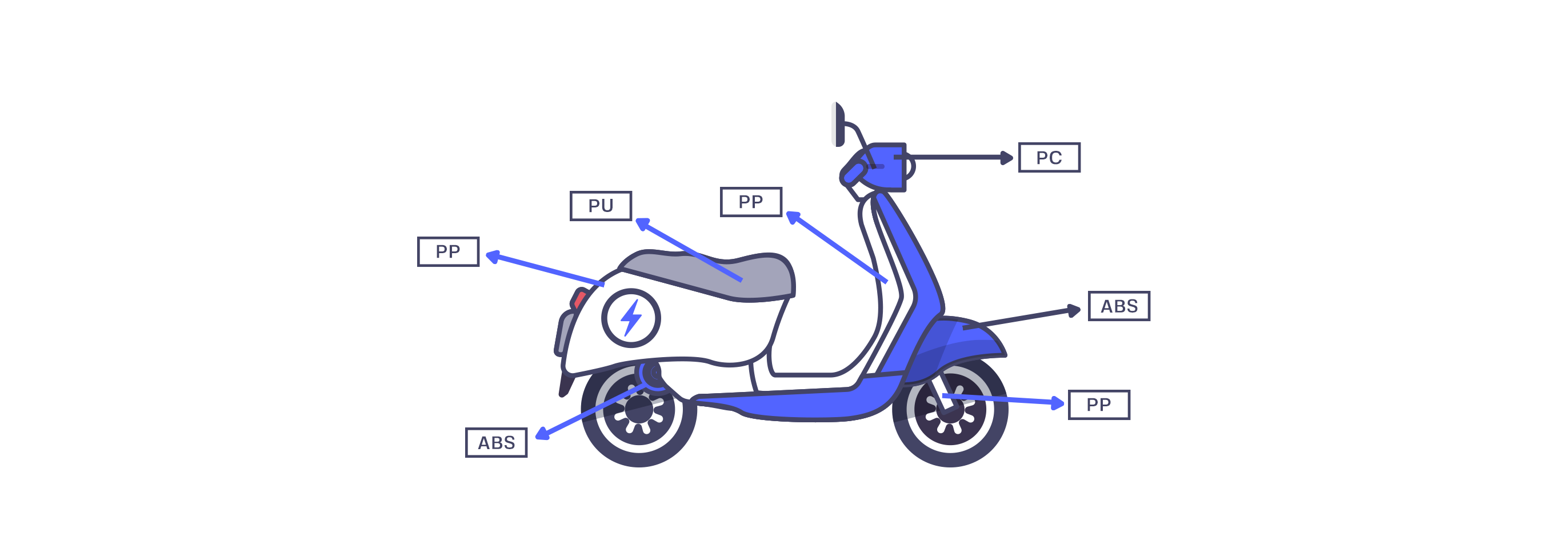
Polyurethane
Polyurethane are the dynamic shock absorbents causing a next level riding experience. Its acoustic dampening decreases the noise offering smooth driving. It offers reduced weight enhancing the fuel economy, electrical insulation, corrosion resistance with increased comfort. Polyurethane foams are used in designing seats, cushions retaining their firmness and resiliency. It also helps to reduce fatigue and stress by even distribution of the weight. Its enhanced fog resistance property is utilized in manufacturing headlights and indicator boards. Its ultraviolet resistance and recyclability can be reduced the overall environmental footprint.
Polyurethane’s excellent resilient properties help to inject mould even the hardest material grades. They are formulated at a temperature of about 248 degrees C. The nozzle has to be maintained with an even amount of heat distributed all over. TPU (Thermoplastic polyurethane) must be processed at a very low temp as it may shrink the final product. The critical step is its drying where the processed parts are examined for their good finish. The moisture has to be removed completely to prevent it from losing its properties gradually.
The heart of an Electric vehicle is its Battery packs. Did you know they are polymers too? What are the important criteria to select them? Let’s help you pick the right one. Follow us for more.